1. 서 론
2. 전력구 현장 디스크커터 마모데이터 분석을 통한 고찰
3. 디스크커터 마모측정 센서 개발
3.1 디스크커터 마모측정 센서 선정을 위한 기초시험
3.2 전력구용 디스크커터 마모측정 센서 설계
3.3 무선통신 및 모니터링 시스템 설계
4. 실대형 굴진시험을 통한 센서 패키지 성능검증
4.1 실대형 굴진시험 설비 및 실험계획 수립
4.2 디스크커터 마모측정 센서 패키지 설치
4.3 실대형 굴진시험 결과 및 성능검증
5. 결 론
1. 서 론
전력구 터널은 안정적인 전력공급을 위한 송전선로 지중화 구조물 중 하나이다. 국내에는 현재 약 232 km 이상 연장의 전력구 터널이 건설되었으며, 이는 송전선로 지중화 사업의 약 12.5%의 규모를 차지하고 있다. 대부분의 전력구 터널은 쉴드 TBM (Tunnel Boring Machine) 공법으로 건설되며, 도달 및 발진수직구를 통해 TBM을 투입하고 반출한다. 주로 연 ‧ 경암 암반을 대상으로 굴착하는 경우가 많은 비중을 차지하고 있다. 암반을 파쇄하는 역할을 하는 디스크커터는 약 2~3 km의 전력구 터널을 건설하는데 약 272~387개가 소모된다. 약 3 km 굴진 시 12억원의 공사비가 투입된다. 디스크커터 링은 굴착하는 과정 중에 지속적인 마모가 발생하고, 약 14~25 mm의 마모한계(17인치 대상)에 도달하게 되면 교체가 필수적이다. 굴진효율과 공사비에 직접적으로 영향을 미치는 디스크커터의 수명을 예측하기 위하여 국내에서도 많은 선행연구들(Jeong et al., 2014; Ko et al., 2014; Kim et al., 2018; 2020d)이 있었다. Park and Song (2022)은 국외 마모예측 모델(Bruland, 1999)과 지하철 터널 현장데이터를 비교하여 각 모델의 예측정확도가 높은 일축압축강도 범위를 분석하였다. 현재까지 국내에서 수행된 디스크커터 마모에 관련된 연구는 굴착효율과 관련되어 공사비와 공기저감 등의 경제적인 기대효과 분석에 초점이 맞춰져있다.
최근 중대재해 처벌 및 지하안전관리에 관한 특별법 시행과 관련하여 사회적으로 안전에 대한 높은 관심과 요구사항이 높아지고 있는 상황이다. TBM은 챔버를 통해 외부 지반과 지하수로부터 안정적인 공간을 확보하여 구조물을 설치한다. 하지만 전력구 건설에 활용되는 약 3.6 m급 소단면 TBM은 더블챔버 이용성이 제한되어 단일챔버로 운영되고 있다. 굴착도구인 디스크커터 마모와 파손상태를 육안으로 확인하기 위해서는 챔버 내부에 있는 굴착토 및 암반버력, 그리고 이수안정액을 모두 제거하여야 한다. 외부 토 ‧ 수압으로부터의 압력 밸런스를 확보하여야 막장면 안전성을 확보할 수 있기 때문에 TBM 챔버 안은 터널 근로자가 작업하기에 많은 위험상황이 도사리고 있다. 이러한 문제를 기술적으로 해결하기 위해서는 디스크커터의 마모 및 파손정도를 무인력으로 측정하는 방법이 필요하다고 판단하였다.
세계적인 수준의 TBM 제작사는 대기압 상태에서 디스크커터를 교체할 수 있는 기술(Accessible Cutterhead)을 개발하거나 커터헤드 전면부에 유압센서를 설치하여 마모상태를 오퍼레이터에게 정보를 제공하고 있다. 또한, 센싱기술을 통해 직접적으로 디스크커터의 마모량을 측정하는 연구들(Lan et al., 2016; 2019; Wang et al., 2019; Fu et al., 2021; Gong et al., 2021)이 진행되었다. 하지만 TBM 챔버 내부는 공간이 매우 협소하고 계측환경이 열악하여 센싱기술을 적용하기가 굉장히 까다롭다. 이러한 극한환경에서 디스크커터의 마모계측을 위해 적용할 수 있는 센서의 종류는 크게 2가지로 조사되었다. Lan et al. (2019)은 와전류 센서(Eddy-current sensor)를 통해 7.95 m Open TBM에 시범적용 하였고, 최대 40 mm의 측정범위와 1 mm 오차범위의 성능을 가진다고 보고하고 있다. Park et al. (2023)은 와전류 센서에 대한 기초시험을 수행하고, TBM에 적용가능성을 평가하였다. Gong et al. (2021) 자기저항 센서(Magnetoresistive sensor)와 LoRa (Long Range) 통신기술을 통해 6.56 m 토압식(Earth pressure balanced, EPB)에 원격 마모측정 기술을 시범적용하였다. 선행문헌에서 소개하고 있는 센싱기술들은 아직 시범적용 단계인 관계로 기술적인 세부내용들이 자세히 공개되어 있지 않으며, 국가별로 TBM의 작업환경이 다르기 때문에 이러한 기술을 국내에 적용하기 위해서는 자체적인 시스템의 개발이 요구되는 상황이다. 따라서 본 연구에서는 이러한 해외의 연구사례를 참고하여 국내 전력구 터널용 쉴드 TBM에 적용가능한 디스크커터 마모계측시스템을 개발하였으며, 이에 대한 개발 내용을 소개하고자 하였다. TBM 디스크커터의 굴착환경을 모사하여 센서후보군에 대한 환경영향성 기초시험을 실시하였고, 시험결과를 바탕으로 디스크커터 마모측정 센서 패키지를 설계하여 시작품을 제작하였다. 시작품이 굴착환경속에서 성능을 발휘하기 위해서 무선통신 방식을 채택하였고, 이를 외부에서 모니터링 할 수 있도록 미들웨어 및 모니터링 시스템도 함께 개발하였다.
2. 전력구 현장 디스크커터 마모데이터 분석을 통한 고찰
Fig. 1은 국내 전력구 터널 현장 2개소에서 디스크커터 점검 및 교체를 위해 챔버를 오픈한 빈도수와 내주(센터, 페이스) 및 외주(게이지) 디스크커터의 평균적인 수명을 비교하여 도시한 것이다. 현장별로 챔버를 오픈한 빈도수는 상이하지만 두 현장의 경우 약 42 m에서 60 m 굴진마다 챔버를 개방하였다. 외주 디스크커터는 119 m에서 124 m 정도 마다 마모한계에 도달하여 교체를 수행한 것으로 분석되었고, 내주 디스크커터는 209 m에서 215 m 정도마다 교체를 수행한 것으로 분석되었다. TBM 건설 중 디스크커터 마모정도나 손상여부를 외부에서 파악할 수 없기 때문에 일반적인 평균 디스크커터 수명 대비 잦은 횟수로 챔버를 개방하는 것으로 분석되었다.
Fig. 2는 전력구 터널 현장 3개소 사례를 바탕으로 디스크커터 위치별(센터, 페이스, 게이지) 마모형태와 교체한 비율을 분석한 결과를 나타낸다. 전력구 A의 터널내경은 3.0 m이며, 커터헤드 직경은 3.55 m로 제작되었다. 커터헤드에는 총 25개의 디스크커터가 설치되어 있으며, 15인치 디스크커터가 사용되었다. 전력구 A 사례에서는 총 261개의 디스크커터가 소모되었고, 디스크커터 교체이력 비율이 센터 13%(34개), 페이스 32%(84개), 게이지 55%(143개)로 분석되었다. 일반적으로 게이지의 교체한 비율이 절반 이상으로 가장 높으며, 센터 1개당 약 4.3회, 페이스 1개당 약 9.3회, 게이지 1개당 약 17.8회를 교체하였다. 마모형태로는 정상마모(Normal wear), 편마모(Uneven wear), 파단(Fracture)로 구분하였다. 정상적인 마모상태가 전체의 76% 이상을 차지하여 주를 이루었다. 전력구 B의 터널내경은 3.0 m이며, 커터헤드 직경은 3.62 m로 제작되었다. 커터헤드에는 총 26개의 디스크커터가 설치되어 있으며, 17인치 디스크커터가 사용되었다. 전력구 B 사례에서는 총 330개의 디스크커터가 소모되었고, 센터 25%(81개), 페이스 18%(60개), 게이지 57%(189개)로 분석되었다. 센터 1개당 약 13.5회, 페이스 1개당 약 5회, 게이지 1개당 약 23.6회를 교체하였다. A 사례와는 다르게 페이스의 교체한 비율이 18% 밖에 되지 않으며, 정상적인 마모상태는 전체의 34%에 그쳤고, 파단의 형태가 35%나 차지하였다. B 사례의 경우, 다수의 파쇄대 구간을 통과하였고, 커터의 높은 경도(HRC 60~61)가 깨짐발생에 영향을 준 것으로 파악되었다(Fig. 3). 전력구 C의 터널내경은 3.0 m이며, 커터헤드에는 총 19개의 디스크커터가 설치되어 있으며, 12 ‧ 14 ‧ 17인치 디스크커터가 다양하게 사용되었다. 전력구 C 사례에서는 총 292개의 디스크커터가 소모되었고, 디스크커터 교체이력 비율이 센터 13%(37개), 페이스 47%(137개), 게이지 40%(118개)로 분석되었다. 센터 1개당 약 9.2회, 페이스 1개당 약 15.2회, 게이지 1개당 약 19.6회를 교체하였다. 페이스의 교체한 비율이 가장 높으며, 정상적인 마모상태가 전체의 59% 이상을 차지하였다.
전력구 터널 현장 3개소 사례를 바탕으로 마모데이터를 분석해본 결과 커터헤드의 설계(프로파일), 디스크커터의 규격 및 설치 위치, 현장별 지반조건에 따라 다양한 마모형태가 발생할 수 있음을 확인하였다. 설계단계에서 마모를 예측하는 것도 매우 중요하지만 터널건설 중 마모를 직접 측정하여 교체를 수행하는 것이 건설관리 측면에서 보다 효율적이고, 챔버개방의 횟수를 줄일 수 있는 방법이라 생각되어 기술개발을 수행하였다.
3. 디스크커터 마모측정 센서 개발
3.1 디스크커터 마모측정 센서 선정을 위한 기초시험
선행연구(Park et al., 2022)에서는 초음파, 와전류, 자기센서에 대한 원리와 TBM 디스크커터 대상 적용사례에 대해 연구동향을 파악하였다. Table 1과 같이 독일, 일본, 중국 세계 많은 국가에서는 다양한 센서선정을 통해 터널현장에 시범구축을 완료하였다. 특히, 중국(Qiuming et al., 2021)의 경우에는 완성도 있는 센서 세트(Integrated sensor set)를 개발하여 마모, 회전 수, 온도까지 측정하였다.
Table 1.
Summary of pros and cons for TBM disc cutter wear sensor candidates
Content |
Candidates Ⅰ: Ultrasonic wave sensor |
Candidates Ⅱ: Eddy-current sensor |
Candidates Ⅲ: Magnetic sensor |
Applications | ![]() | ![]() | ![]() (Qiuming et al., 2021) |
Principle of sensor | ![]() (Park et al., 2022) | ![]() (Spurek et al., 2021) | ![]() (Qiuming et al., 2021) |
Advantages | • Easy to install and use |
• High precision • No influence on measurement environment |
• Sufficient measuring distance • No influence on measurement environment |
Disadvantages |
• Influence on measurement environment • Low precision |
• Relatively short measuring distance |
• Requirement of external magnet installation |
초음파 센서(Ultrasonic wave sensor)는 초음파의 속도와 이동시간을 기반으로 디스크커터 링과 센서와의 거리를 측정하는 원리를 가지고 있다. 초음파 센서를 활용한 디스크커터 마모측정 센서는 독일 TBM 제작사인 헤렌크네히트(Herrenknecht)사에서 개발이 완료 된 것으로 알고 있으며, 이는 중 ‧ 대단면 TBM에서 적용할 수 있는 대기압 상태 디스크커터 교체 시스템이 있기 때문에 초음파 센서를 통해 마모량을 측정 할 수 있을 것으로 생각된다. 초음파센서는 대기 중에서 변위를 측정하기 위한 것으로 수십 kHz의 주파수대역대를 사용한다. Fig. 4와 같이 초음파 센서 대상으로 수중환경, 이수안정액 환경, 토사환경에서 측정을 시도하여 보았지만 해당 주파수의 음파는 공기 이외의 매질을 투과하지 못하기 때문에 측정이 불가하였다. 이에 전력구 내경 3.0 m에서 4.5 m 사이의 단면이 작은 전력구 건설용 TBM에서 적용하기 어려울 것으로 판단하고 있다.
와전류 센서의 경우에는 국내 연구진(Park et al., 2023)에 의해서 적용성이 검토되었다(Fig. 5). 와전류 센서는 토사, 이수액, 수중 환경에서 측정결과의 영향을 받지 않은 것으로 확인되었지만 Fig. 6과 같이 실제거리와 측정거리가 선형적인 관계를 가지는 최대거리가 약 16 mm로 다소 짧아 디스크커터의 한계마모를 모두 측정하기에 추가적인 검토가 필요할 것으로 판단되었다(Park et al., 2023).
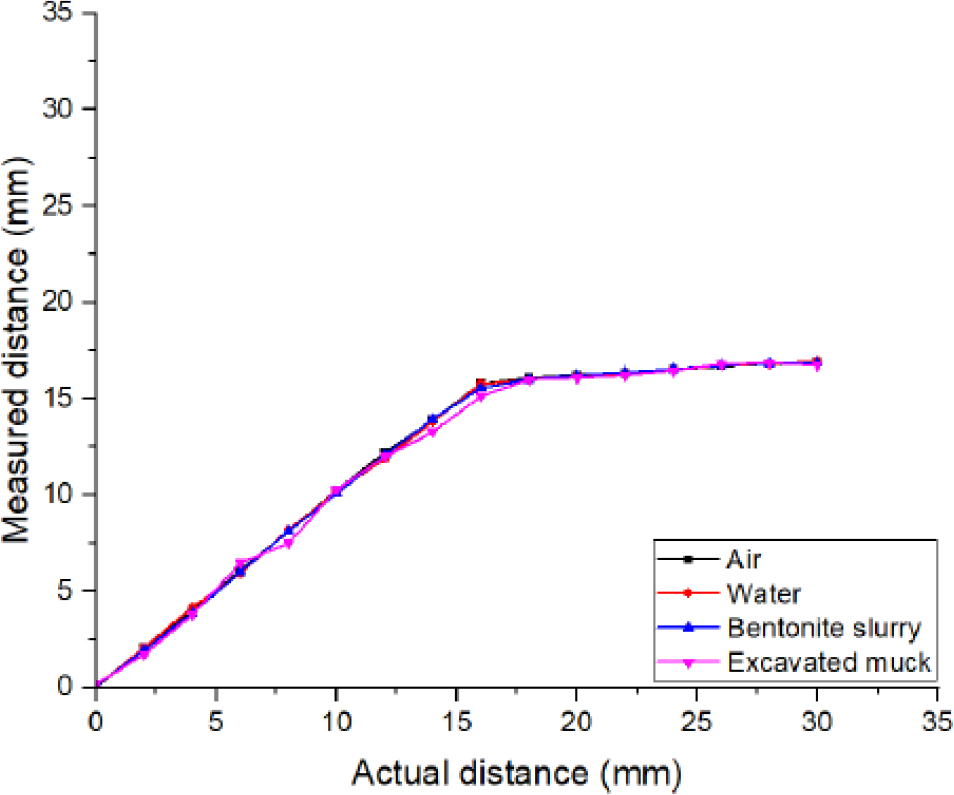
Fig. 6.
Comparison results of distance measurement in different conditions using eddy-current sensor (Park et al., 2023)
한편 자기센서는 자기장 또는 자기력선의 세기를 홀효과(Hall effect)에 기반하여 전압으로 환산하여 출력하는 센서이다. 자기센서를 통해 디스크커터의 마모량을 측정하는 원리는 다음과 같다. 센서와 측정대상 물체 사이에 형성된 자기장은 센서와 측정대상과의 거리에 따라 자속밀도(Magenetic flux density) 크기가 변화하며, 이러한 자속밀도의 변화는 전압값으로 출력된다. 이때의 출력전압과 거리(센서-측정대상)와의 상관관계를 이용하여 특정한 전압값이 지시하는 거리를 계측할 수 있다. 한편 디스크커터는 챔버 내에 위치하여 다양한 굴착환경에 노출되므로 이러한 환경에서 센서의 계측성능을 확인하는 것이 중요하다. 본 연구에서는 Fig. 7과 같이 수중, 이수안정액, 그리고 토사환경에서의 자기센서의 측정가능성을 확인하고자 하였고, Fig. 8은 자기센서를 통해 측정된 계측거리와 실제거리를 비교하여 도시한 것이다. 실내시험을 통해 자기센서는 모든 환경에서 거리 측정이 가능한 것을 확인하였고, 환경에 따라 계측성능은 큰 차이를 보이지 않는 것을 알 수 있었다. 또한 자기센서는 최대 60 mm까지의 거리를 측정할 수 있었으며, 대기, 수중, 이수안정액, 토사에서의 계측정확도는 각각 97%, 98%, 95%, 90%로 나타나 모든 환경에서 우수한 계측성능을 보이는 것으로 분석되었다.
3.2 전력구용 디스크커터 마모측정 센서 설계
디스크커터 마모를 측정하기 위한 센서 패키지를 설계하기 위해서는 마모량 측정방식, 전원공급 방식, 유 ‧ 무선통신 방식, 챔버안 내구성 확보방안, 디스크커터 홀더와의 결합방식에 대한 고려가 필수적이다. 본 연구에서는 마모량 측정방식으로는 앞선 3.1절 결과를 바탕으로 자기센서의 적용성이 가장 우수하다고 판단하여 Fig. 9와 같이 자기센서를 활용한 디스크커터 마모측정 센서 패키지를 설계하고자 하였다. 자기센서는 측정부가 디스크커터 링과 정면으로 측정할 수 있도록 설계하였다. 자석의 위치는 자기센서 바로 후면에 설치하여, 디스크커터 링과 자기센서와의 최대 측정거리는 45 mm까지 가능하였다. 자기센서 자체로도 최대 100 bar까지 대응가능하며, 내해수성의 성격을 지니고 있다. 자기센서는 출력 전압으로 마모량을 산출하며 출력 범위는 2~10 V로 값을 출력하고, 지그비 무선통신(Zigbee wireless communication)을 통해 디스크커터에서 챔버 외부에까지 신호를 전달한다. 자기센서는 11.5~30 V의 전원을 사용할수 있으며, 전원공급의 경우에는 리튬이온 배터리 18650를 4P4S (4열4행 직열+병렬 조합)로 사용하였으며, 배터리용량은 10,400 mAh이고 출력전압은 14.8 V이다. 마모센서 패키지 시작품으로 하루 24시간 기준 약 3일 정도의 전원공급용으로 별도의 On/Off 제어는 수행하지 않았다.
Fig. 10과 같이 디스크커터 마모측정 센서 패키지를 외부 버력과 토 ‧ 수압으로부터 센서 및 내부장치를 보호하기 위하여 일반구조용 압연강재 SS275를 이용하여 최대 토 ‧ 수압 9 bar에 대응할 수 있도록 두께를 설계하였다. 디스크커터 홀더방식에 결합이 원활할 수 있도록 센서 패키지의 크기는 폭 360 mm, 높이 206 mm로 설계하였으며, 무게는 14 kg으로 도구없이 인력으로 운반이 가능하도록 하였다. 개발한 자기센서 케이싱은 가능한 2~3 km 터널 프로젝트 내에서 내구성 확보를 목표로 하며 내부 센서, 배터리, 통신모듈 모두 안전성을 확보하도록 설계하고자 하였다. 상부 케이싱에는 전원공급 배터리와 통신모듈이 위치하고 있으며, 하부 케이싱에는 자기센서 등이 위치하고 있다. 두 케이싱은 4개의 볼트로 결합되고, 물이 유입되는 것을 방지하기 위해 실리콘 막음처리를 진행하였다.
3.3 무선통신 및 모니터링 시스템 설계
Fig. 11은 디스크커터 마모측정 패키지의 무선통신 및 모니터링 시스템의 개념도이다. 개별 디스크커터 마모측정 센서 패키지로부터 측정된 전압(mV 또는 마모량)에 대한 정보는 디스크커터 마모측정 센서 패키지 내부 아두이노 보드에서 취득된다. 지그비 무선통신 모듈(XBee S2)을 활용하여 챔버를 통과하여 TBM 내부로 수신되게 된다. 개별 디스크커터 마모측정 센서 패키지를 송신기로 구분하고, PLC (Programmable Logic Controller) 통신박스(Fig. 12)와 통신하는 아두이노 보드는 수신기로 구분한다. 다수의 송신기는 마모측정 센서로부터 측정된 값을 한 개의 수신기로 전달한다. 수신기와 PLC 통신박스 간의 연결은 통신박스 내의 산업용 미니 PC USB 포트를 통하여 연결되며, 시리얼 통신을 사용한다. PLC 통신박스에서는 시리얼로 수집된 데이터를 내부 데이터베이스 관리 시스템(Data Base Management System)에 우선 저장한다. 내부 DBMS에 우선 저장하는 것은 오프라인(Offline) 환경에서도 데이터를 수집하기 위함이며, 이후 수집 프로그램 내에서 네트워크가 온라인(Online)임을 확인하고, 내부 DBMS에 저장된 데이터를 외부 DBMS에 저장한다. 이때 직접 DBMS에 접속하지 않고 웹서버(Web server)를 이용하여 보안성을 향상시켰다. 외부 DBMS에 저장된 센서별 측정값은 Fig. 13과 같이 모니터링 시스템 실시간으로 정보를 사용자에게 제공할 수 있다.
4. 실대형 굴진시험을 통한 센서 패키지 성능검증
4.1 실대형 굴진시험 설비 및 실험계획 수립
선행연구(Kim et al., 2020a; 2020b; 2020c)들을 통해 실대형 굴진시험 설비에 대한 소개와 관련된 실험결과 분석이 이루어졌다. 본 연구에서는 Fig. 14의 3.6 m급 토압식 TBM을 활용하여 굴착환경에서 디스크커터 마모센서의 측정 및 무선통신 가능성 분석을 위해 실대형 굴진시험을 추진하게 되었다. TBM 굴착에 따른 챔버 내 버력과 먼지, 그리고 커터헤드와 메인바디(강재) 속에서 센서측정과 무선통신에 대한 성능을 검증하는 것이 중요하다고 판단하였다. 또한, 진동 속에서 디스크커터 마모센서의 설치 및 내구성에 대한 성능검증도 이루어졌다. 인공암반의 크기는 87.5 m3 부피이며, 일축압축강도 27 MPa의 콘크리트를 활용하여 조성하였다.
TBM이 굴진하는 메커니즘 안에서 디스크커터 마모측정 기술에 대한 성능검증이 이루어졌다. 실대형 굴진시험을 위하여 시험조건은 Table 2와 같이 쉴드잭의 추력과 커터헤드의 회전속도(RPM)로 산정하였다. 비교적 약한 암반강도를 고려하여 추력은 1,000 kN과 3,000 kN으로 구분하였고, 회전속도는 1.5 RPM으로만 굴진시험을 수행하였다. 약한 강도에서 높은 추력은 큰 토크를 야기시키고, 회전속도를 일정하게 유지하기 어렵기 때문에 제한적으로 1.5 RPM만 수행하였다.
Table 2.
TBM operational parameters for tunnelling tests
Test cases | Operational parameters | |
Thrust force (kN) | RPM (rev/min) | |
#Test 1 | 1,000 | 1.5 (1 pump, 90 kW) |
#Test 2 | 3,000 | 1.5 (1 pump, 90 kW) |
4.2 디스크커터 마모측정 센서 패키지 설치
토압식 TBM 부품 중 S355J2+N 강재의 단조형 커터헤드가 실대형 굴진시험에 활용되었고, 17인치 디스크커터 25개로 구성이 되어있다(Fig. 15). 디스크커터간 절삭간격은 84 mm와 85 mm로 제작되었다.
Fig. 16과 같이 디스크커터 마모측정 센서 패키지 하부 케이싱에는 디스크커터 홀더체결 볼트홀이 제작되어 있다. 페이스와 게이지 디스크커터에 적용가능한 마모센서의 경우에는 디스크커터 고정용 웨지를 설치한 상태에서 웨지 볼트에 마모센서를 위치시켜 와셔와 너트를 체결하고, 커버를 체결하면 설치가 완료된다. 디스크커터 교체 시 마모센서 패키지도 동시에 분리 및 결합 할 수 있어 매우 간편할 뿐만 아니라 여러 제작사의 TBM에서도 동일한 홀더 타입을 채택하고 있어 범용적으로 적용할 수 있는 장점이 있다. 디스크커터 마모센서 패키지를 센터커터와 페이스 및 게이지커터 위치에 각각 설치한 모습을 나타내었다. 본 실대형 굴진시험에서는 총 8개의 디스크커터 마모측정 기술 시작품을 제작 하였으며, 디스크커터 4번, 7번, 10번, 16번, 18번, 19번, 22번, 24번에 설치하였다(Fig. 16). Fig. 17은 디스크커터 22번에 설치된 마모측정 센서 패키지의 모습을 확대하여 제시하였다.
4.3 실대형 굴진시험 결과 및 성능검증
본 연구의 실대형 굴진시험에서는 TBM의 굴진성능에 대한 평가보다는 개발된 디스크커터 마모센서의 안정적인 측정환경을 제공하는 것에 초점을 맞추었다. Fig. 18은 Test #1 (추력: 1,000 kN, RPM: 1.5)에서 측정된 TBM의 추력, 토크, RPM을 보여준다. Fig. 18(a)와 Fig. 18(b)에 나타난 바와 같이, 목표로 한 1,000 kN의 추력과 1.5 RPM이 안정적으로 유지된 것을 알 수 있다. Fig. 19는 Test #2 (추력: 3,000 kN, RPM: 1.5)의 경우이며, 앞선 Test #1과 마찬가지로 목표로 한 3,000 kN의 추력과 1.5 RPM이 안정적으로 유지된 것으로 확인되었다.
본 실대형 굴진시험은 약 100 mm 이내의 굴진거리를 굴착하기 때문에 굴진시험에 따른 디스크커터의 마모는 발생하지 않는다. 따라서 마모센서가 지속적인 굴착환경에서 안정적으로 측정이 가능한지를 확인하는 것에 초점을 맞추었다. Test #1의 경우 Fig. 20(a)와 같이 총 8개의 센서 패키지에 대해 5개가 정상적인 측정결과를 보여주고 있다. 5개의 센서를 통해 평균 5,239 mV에서 7,083 mV까지 범위의 전압이 측정되었고, 전압값은 굴착 도중 큰 변화(오차범위 ±10 mV)를 나타내지 않았다. 그러나 7번 커터에 장착된 센서의 경우, 전압이 2 mV로 사실상 측정이 되지 않았으며, 10번 커터에 장착된 센서의 경우는 무선통신 상태가 불량하여 지속적인 측정이 어려웠다. 22번 커터에 장착된 센서의 경우는 최소 4,261 mV에서 최대 4,408 mV까지 다른 센서에 비해 측정된 전압의 변동이 가장 큰 것으로 계측되었는데, 이는 실험 후 계측센서의 결선불량으로 발생한 것으로 확인되었다. 각 센서별 측정된 전압의 크기가 상이한 이유는 센서와 디스크커터 거리와의 차이가 다소 발생할 수 있고, 자기센서와 하부케이싱 돌출부와의 설치오차에 따라 영향을 받았다고 생각된다. 자기센서를 둘러싸고 있는 설치환경이 측정값에 영향을 줘 초기값이 달라질 수 있어, 향후 이에 대한 보완연구를 수행할 계획이다.
Fig. 20(b)는 Test #2에서의 센서 패키지 데이터를 도시한 것이다. 쉴드잭의 추력이 3,000 kN으로 증가한 Test #2의 경우는 Test #1에 비해 1개의 센서가 더 무선통신 상태가 불량하게 나타났다. 정상적인 작동을 하는 센서의 경우는 Test #1과 동일한 측정결과를 보여줬다. 4개의 센서결과는 평균 5,239 mV에서 7,079 mV까지 범위의 전압이 측정되었다. 7번 커터에 장착된 센서의 경우 사실상 측정이 되지 않았으며, 10번과 19번 커터에 장착된 센서의 경우는 무선통신 상태가 불량하여 지속적인 측정이 어려웠다.
디스크커터의 마모량은 변화된 전압의 값(∆ mV)을 통해 마모량(∆ mm)으로 환산할 수 있는데, 앞선 3.1절의 기초시험(Fig. 8)에서 설명한 바와 같이 측정된 전압의 값과 실제 거리와의 상관관계를 통해 계산할 수 있다. Fig. 21은 굴착시험 도중 정상적인 계측이 이루어진 것으로 판단되는 일부 센서들(4번, 16번, 18번, 24번)만의 계측전압과 전압변화량(∆ mV)을 나타낸 것이다(Test #2). 본 굴착시험의 경우 디스크커터의 마모가 발생하지 않아 ∆ mV이 오차범위인 ±10 mV 내에서 계측된 것으로 확인되었으며, 이러한 오차범위를 거리로 환산하면 약 ±0.1 mm이다. 이에 따라, ∆ mV를 통해 환산된 마모량은 시험 도중 0에 가까운 값으로 도출되므로 이에 대한 분석결과는 생략하였다. 일련의 굴착시험을 통해 디스크커터 마모계측 시스템에 설치된 자기센서는 굴착환경속에서 디스크커터와의 거리를 안정적으로 계측하는 것으로 확인되었고, 계측된 데이터는 무선통신을 통해 원활하게 수집됨을 검증하였다. 한편 Fig. 22는 시험이 종료된 이후 디스크커터 마모계측 시스템의 사진을 나타내며, 센서 패키지의 이탈, 파손 등이 발생되지 않고 안정적인 계측환경을 제공할 수 있었던 것으로 판단된다.
Fig. 22와 같이 실대형 굴진시험을 통해서는 디스크커터 마모측정 센서 패키지 이탈, 파손 등 어떠한 손상도 확인할 수 없었다.
5. 결 론
본 연구는 전력구 터널 건설에 활용되는 TBM에 적용할 수 있는 디스크커터 마모측정 기술을 개발하여 굴착환경에서 마모량 측정, 무선통신, 내구성을 확보할 수 있는지에 대한 성능검증을 수행하였다.
1. 전력구 터널 건설과정 중 발생한 디스크커터 마모데이터를 분석한 결과, 디스크커터 수명 대비 챔버 개방의 횟수가 많고, 다양한 지반조건에서 디스크커터의 설치위치별(센터, 페이스, 게이지) 상이한 마모특성을 나타내어 실질적인 계측기술 개발을 통해 챔버 내 안전과 굴착효율 향상을 통한 경제적인 효과를 기대할 수 있다.
2. 굴착환경속에서 디스크커터를 원격으로 측정하기 위해서 적정센서 후보군을 고찰하고, 기초시험을 수행한 결과 자기센서가 가장 적합하다고 판단하였다. 디스크커터의 마모한계를 고려한 측정거리(45 mm) 확보와 굴착환경(이수안정액, 토사)에서의 측정여부 고려하여 초음파 및 와전류 센서보다 적합하였다. 자기센서를 바탕으로 전원공급, 무선통신을 종합한 디스크커터 마모측정 센서 패키지를 설계하였다.
3. 최대 3,000 kN의 추력과 1.5 RPM의 획전속도로 굴착하는 실대형 굴진시험 조건에서 자기센서 측정, 무선통신 모듈(지그비), PLC 통신박스의 데이터 송 ‧ 수신, 모니터링 시스템의 데이터 표출이 모두 유기적으로 성능을 확보하는 것으로 분석되었다. 통신이 원활하지 못했던 센서 패키지의 경우는 패키지 조립과 터미널 단자의 결합불량으로 향후 보완을 거쳐 완성도 있게 제작을 수행할 계획이다.
4. 토압식 쉴드 TBM이 활용된 실대형 굴진시험에서는 버력과 먼지, 그리고 강재로 둘러싸인 밀폐공간에서의 시작품의 성능을 검증하였다. 다만, 토압식 쉴드 TBM을 밀폐형으로 운영하지 않았기 때문에 대기압 조건에서의 검증에 해당한다. 이에 향후, 이수안정액과 이수가압식 쉴드 TBM 환경에서 추가적인 성능검증을 수행할 계획이다.